Home > Wooden Boats- Resins & Coatings
Coatings, Resins, and Preservatives
The treatment of wood for the purposes of protection and preservation fall into four general categories: Coatings, resins, bactericides/fungicides, and “Preservatives”.
Coatings: All wood boats need coatings of some sort if they are going to last, even if the coating is only one of the natural oils such as linseed oil.
Coatings include paint, which is the most common form of wood protection. All paints are pigmented and therefore assure good UV light protection. Most paints are more or less waterproof, as long as the surface remains unbroken. Paint will pass some air and some moisture, so it does not restrict the ability of the wood to “breathe”, that is, absorb and emit gasses/moisture as environmental conditions change. In many types of boat construction the ability of the wood to breathe is an important factor.
Paints have different general bases, which include the basic oil base, the more recent water-base, and finally synthetic or polymer bases (or oil-based paints which include polymer ingredients), such as acrylics and polyurethanes. The choice of paint depends on application area, boat usage, intended appearance, and your budget. There are some extremely high-gloss polymer paints that are best sprayed over the surface in a environmentally controlled building. It’s a costly process and only used on wood that is in almost perfect condition. Manufacturers are generally very specific about where and how their paint should be used. Our Rhino Top, for example, is an epoxy/acrylic water-based paint that is especially suited for flat, trafficked surfaces, and that is what we advertise it for. Read paint labels carefully before deciding if they are appropriate for your application.
There are clear coatings as well, and these include the varnishes and clear urethanes. For marine use the standard clear urethanes are rarely used, largely because they contain no (or very little) UV inhibiting chemistry. Varnishes are the common clear coating for marine use, and any marine-grade varnish will have a lot of UV inhibiting chemistry. UV chemistry is expensive, one of the reasons why marine varnish costs more than a standard store varnish. Varnishes are also “natural” oil base, or may include some synthetics such as polyurethanes. We carry a Marine Spar Varnish available in gloss and satin finishes.
There are some newer activated polyurethane coatings, which are like paint only in the sense that they are opaque and can be brushed on the surface. These are “soft-cure” (they remain somewhat flexible, much more so than the polyester and epoxy resins) and are generally waterproof and have long durability, some exceeding 15 years. The toughest one we know of is the ELASTUFF™ 120, which for marine use is basically a very tough base-coating. It can be top-coated with Rhino Top (for decks) or the other polyurethane coating we carry, Elasta-Tuff™ 6000-AL-HS (for cabins and hulls). The Elasta-Tuff™ 6000-AL-HS can also be used by itself as a very tough, durable and non-fading surface coating.
Resins: There are pure hard-curing resins that can be used to coat wood, although they almost always require some type of opaque top-coating for UV protection after they have cured. Basically, these resins fall into two categories, polyester resins and epoxy resins. Polyester resins are what fiberglass boats are constructed from, and they are used because they are relatively inexpensive and they set quickly. Polyester resins do not bond very well to wood, and we recommend that they never be used for this purpose. Epoxy resins do bond well with wood and can be used to coat a boat hull if conditions are exactly right: Intact, dry wood that is in good condition, and the resin laid down with a woven fiberglass cloth.
Bactericides, Fungicides and “Preservatives”: Some paints and coatings have bactericides/fungicides as part of the mix, and the manufacturer will say so on the container. Other types of products are by their very nature fungicidal and bactericidal, but can’t promote this fact because of EPA restrictions regarding these kinds of claims without being extensively tested and subsequently listed as a “Pesticide”. The whole issue can be a little confusing, and is under constant review and revision by appropriate state and federal agencies.
Wood that has been pre-treated with fungicidal/bactericidal chemistry (such as copper naphthenate) varies considerably in it’s effectiveness, depending on the particular toxicity of the chemistry and the method by which it was applied. Generally speaking, wood so treated can be considered “preserved” as long as it is not cut or drilled into. Once cut or drilled, untreated inner wood is exposed and is vulnerable to rot fungi and bacterial activity. Of course, the newly exposed wood can be treated with a fungi-bactericide. These chemistries are available in hardware and home stores, and range from common creosote to some more exotic and refined concoctions.
The borate products (various forms of disodium octaborate tetrahydrate) will protect wood from rot, and if applied to rotted wood will stop the deterioration process. In bulk, the pure disodium octaborate tetrahydrate powder is relatively inexpensive and non-toxic. It can be mixed with warm water and sprayed on the wood surface. The big disadvantage of the borates is that they eventually leach out of the wood. They have to be re-applied at regular intervals. A powder-water mix will have no effect on subsequent coatings, such as epoxies and paints.
Finally, there is antifreeze with its glycol base. Claims are made that this is a bactericidal/fungicidal mix, although it is not approved for this by the EPA. Assuming that the claims are correct, the glycols have the same problem as the borates, that is, they eventually leach out of the wood, and have the added problem of contaminating the wood with glycol. No manufacturer of surface coatings or bonding agents of any type will guarantee their product’s effectiveness on a surface that has been treated with antifreeze. We do not recommend its use.
The word “Preservative” is essentially a meaningless term, since everyone who makes anything that goes on wood can call it a “preservative”. Some work better than others, but none are “permanent”, with the exception of the S-1™ Clear Penetrating Epoxy Sealer. The S-1™ Clear Penetrating Epoxy Sealer soaks into the the wood as deeply as possible, filling any small spaces between the wood fibers with a premium epoxy resin. For Larger cracks or voids, the Sculpwood® epoxy fillers, the Putty or Paste and/or the General Purpose Epoxy™ Resin is required for a complete structural repair. Nothing that we know of beats epoxy, so the wood is generally protected against deterioration. All the product testing we have done reinforces this.
Repairs Using Resins and Coatings
The use of paints, resins and coatings on boats requires careful and thorough preparation. Lack of proper preparation, in the use/mixing of the products and the preparation of the surface, is the most common cause of disappointment and failure in the final result. Carefully read the package labeling, the instruction material supplied with the order, and if in doubt, ask questions! At The Rot Doctor™ we always have technical support available, 6:30 AM to 5:30 PM Pacific time by phone weekdays and 8:30 AM to 5:30 PM Pacific time weekends and holidays, and by email, which is always answered within 24 hours.
Effective Use of Resins: We mentioned above that polyester resins should never be used in the repair of wooden boats because it’s brittle, lacks strength, and it lacks the ability to bond well with wood… and we’re saying it again now. There are a few instances where polyester resin has worked in sheathing under some very special circumstances, but there are many, many more instances where it has failed. It’s only advantage is that it is inexpensive, which isn’t worth much when you consider the amount of time you put into making the repair. That said, we turn to epoxies, clearly the chemistry of choice for wood boat repairs. Epoxies are formulations, and they are formulated by the manufacturer to accomplish certain results and to be marketed at a certain price point. Epoxies are not all the same: Some are quick-setting, some slow-setting, some for broad laminations, some for specific repairs, some brittle and shattering, some more flexible. We offer the General Purpose Epoxy™ Resin with three temperature formulations you can choose the right one based on minimum temperatures expected during application and desired pot life.
Epoxy resins can be mixed with other dry substances, such as wood flour, talc, glass fibers, micro-balloons, etc. to increase thickness. The Sculpwood® Moldable Epoxy Putty is a thick putty that can fill large cavities even on vertical or overhead applications. The Sculpwood® Epoxy Paste is a thinner product that is easily pushed into small cracks or crevices. They can also be used in conjunction with each other for better bonding of the putty to the wood, they are both strong and easily sanded.
For gluing and bonding the same wide variety of epoxy formulations exist. Marine-grade epoxies are superior to standard epoxies, but even here there are wide variations. Some are not effective in temperatures below 50 F/10 C, and some will not bond the more “difficult” woods, such as teak, white oak and the dense, oily hardwoods. We offer 2 epoxy adhesives both are effective in lower temperatures and work well with oily woods. The T-88® Structural Epoxy Adhesive is better used for laminations and the G-2™ Epoxy Adhesive is better used for joints and gap filling situations.
S-1™ Clear Penetrating Epoxy Sealer is a deep penetrating epoxy. It will harden soft wood, and it will prevent further rot or deterioration, and it will help protect new wood from deterioration and delamination. It is also the perfect bonding base for epoxy resins and fillers, as well as paint and coatings.
Effective Use of Coatings: Coatings are generally a high-end means of achieving waterproofness, wear-resistant characteristics, and good UV protection for the wood. The good ones are expensive, and are usually activated formulations. The most effective coatings are almost always opaque.
With coatings it generally doesn’t pay to be too price-sensitive, because you truly get what you pay for. Our Rhino Top, for example, is a third of the price of the Elasta-Tuff™ 6000-AL-HS, but the Rhino Top is basically a water-based high-end paint, while the Elasta-Tuff™ 6000-AL-HS is a polyurethane formulation that has completely different characteristics. Be cautious when shopping at the home stores where performance promises are generous and detailed product information is scarce.
Preparation is essential with coatings. The surface must be exactly to manufacturer’s specifications, and application procedures followed exactly. Our Elastuff™ 120, for example, is an extremely durable activated polyurethane coating, but can be difficult to apply. For wooden boats most coatings are for deck and cabin top protection and waterproofing, and all previous material must first be removed and the wood treated in preparation for the coating. We believe that no coating should be laid down over a wood surface without first treating the surface with the S-1™ Penetrating Epoxy, because the S-1™ Penetrating Epoxy is so effective in increasing bonding ability of the coating and in protecting the wood from future rot and deterioration.
Types of Repairs
Basically, these can be divided into two categories, surface repairs and structural repairs.
Surface repairs assume that the basic structure of the area to be repaired is sound and treatment is required only to stop wood deterioration or to fill areas where some wood is missing. It’s important to be sure that the structure is sound before repairing the surface. Deteriorated wood on the surface can mean that there are more serious problems underneath. On planking and cabin sides the deterioration may have gotten to the frames underneath, and this must be evaluated in advance. The structural repairs must be made first, and then the surface can be attended to. Fastenings (nails, screws, bolts) should be checked for soundness and replaced if necessary.
The S-1™ Clear Penetrating Epoxy Sealer is the premium product for use in surface repairs. It will harden soft wood, assuming that the fibers are all in place it maybe all you need, although several coatings to the deteriorated area are sometimes required. The S-1™ is always recommended on deteriorated wood before using a thicker epoxy to fill in any missing wood. The S-1™ Penetrating Epoxy is often freely used on fastening holes to restore the wood. On window/port framing it can be a valuable means to harden the wood and prevent further deterioration.
For surface repairs, a epoxy resin is a good adjunct to the S-1™ Penetrating Epoxy, providing a deeper fill in areas where the wood is “loose” and fibers are missing. The General Purpose Epoxy™ Resin works great as a pourable filler and can be mixed with dry additives to thicken it or used without thickeners to glue the “loose” fibers back into place. For filling in missing areas, the Sculpwood® Moldable Epoxy Putty is a thick putty that can fill large cavities even on vertical or overhead applications. The Sculpwood® Epoxy Paste is a thinner product that is easily pushed into small cracks or crevices. They can also be used in conjunction with each other for better bonding of the putty to the wood, they are both strong and easily sanded. All of these products will bond chemically with the S-1™ Penetrating Epoxy treated wood.
One of the most successful stories of surface restoration came from one of our customers, the owner of Sanzone, a 37′ mahogany planked Sportsfisher built in 1961. The results are truly beautiful. In his own words, here is an excerpt from our Customer Projects article, Sanzone: A Brief History and Refit Story…
![]()
“Once the hull was bare and all seams clean and ready for new caulk we checked and tightened or replaced any fasteners that needed attention. The wood hull was without many soft spots, at least none that were structurally damaging. This moved us to the next stage.
I worked with the CPES™* (Clear Penetrating Epoxy Sealer™) on some new wood being prepared for the bridge and cabin sides and was very pleased with the results. I felt it was worthwhile to apply CPES™* to the entire hull prior to caulking and painting. I knew from talking to others and reading positive reports about this mixture that it would insure longevity of the wood and prep the surface for a superior bond for the adhesive caulk to the seams. I also knew that this process would only need doing once, and that it would solidify the grain in the wood hull.
The adhesion was very good when applying caulk over hull materials that had been treated with CPES™*. Above the waterline we used 3M 5200 sealant and 3M 4200 sealant below the waterline over the new seams.
I decided the hull would finish smooth rather than with revealed seams between planks. To rout the seams again to bring plank definition back would have meant another few weeks added to the project and I liked the idea of a smooth sided hull. We fared the seams using the 2-part Fill-It™ Epoxy Filler* as a faring compound. It was mixed and applied to the seams with good results. It took some time with re-application and sanding to get her as smooth as possible, but the results are good and this hull is well sealed and strengthened. As you can see by the after-paint photos, it was a worthwhile step.”
Read the rest of Sanzone: A Brief History and Refit Story in our customer projects section which includes many more photos of the project from start to finish.
* These products are unavailable, we are selling comparable products that will perform these same tasks. Feel free to contact us if you need assistance with which products to use.
Structural repairs have traditionally been made by replacing wood. This is fine and we agree that it is the best method, and we will only add that treating all new cut/trimmed wood going into the boat with the S-1™ Clear Penetrating Epoxy Sealer will help protect it against rot and deterioration.
Unless one is a good woodworker with the right tools and the time, these repairs are often left to the shipwrights. And this gets expensive! When we bought the 1889 tug Delta, the horn timber was 50% rotted away. Repair estimates by shipwrights started at a $20,000 base, and they admitted that it would probably cost more. Why? Because replacing the timber would have meant tearing the stern off the tug, replacing the horn timber, and then rebuilding the stern. Authenticity of the boat was hardly the issue, because the whole stern would have been basically new wood. We repaired it ourselves with CPES™*, Layup & Laminating™ Resin* and sawdust, and Fill-It™ Epoxy Filler*. It took about $500.00 worth of our epoxies and 30 hours of labor, and the “timber” is probably stronger now than it was originally. That is the logic of making structural repairs with premium epoxies. You can read more about this repair in our Rotten‘Zine, Delta’s Horn Timber: Fixing it on the cheap.
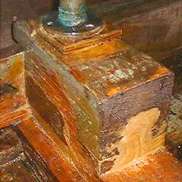
After
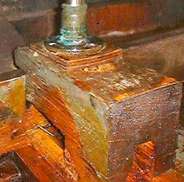
Before
The owner of the Leprechaun sent us these pictures (right) of his steering shaft block/horn timber repair using the same methods we used for Delta. The before picture shows the horn timber with the rot dug out. The after picture shows the result after treating the wood with CPES™* and filled with a mixture of wood flour and L&L Epoxy Resin*. These are permanent repairs that will last, and the cost to the boat owner was less than $200.00 in materials. You can see pictures of Leprechaun’s Horn Timber and Stern Plank Repair in our customer projects section.
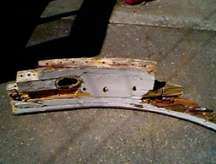
It’s sometimes surprising how much can be repaired with epoxies. Here are pictures (left) showing the repair of a stern bulwark where the wood was actually pulled away, restored, and then replaced. Here is an excerpt from our customer projects section, Fixing Puff.
“I took a torch and burnt off all paint so I could see what I was dealing with. For safety, I had a bucket and hose near by. I also had a helper man the hose, and stay on the look out. I would not have tried this if I had gasoline or propane on board.
The stern section was soaked in CPES™*, and filled with Layup and Laminating™ Epoxy Resin*. The broken off piece was attached using 8 inch galvanized lag screws.
![]()
Layup and Laminating™ Resin* was poured in both ends of the broken bulwark to form a tight bond between the broken bulwark and the bulwark attached to the boat. Vacant spaces were then filled with Fill-It™ Epoxy Filler*.
I applied two coats of CPES™* the day before applying the white enamel. The CPES™* was applied to make the bulwark more water resistant.
![]()
This (near left pic) is actually a close up of the section that I broke off, after the repair was complete. I had to take a look at the picture a few times myself. From this picture you would never know that this section had broken off.”
Read the entire article on Fixing Puff which also includes a bow repair in our customer projects section.
* These products are unavailable, we are selling comparable products that will perform these same tasks. Feel free to contact us if you need assistance with which products to use.
However, there are limitations on what and how much can be repaired using epoxies. Large areas of deterioration on planks means that the plank and the fasteners should be replaced with new wood. The framing underneath can often be repaired using the S-1™ Clear Penetrating Epoxy Sealer and fillers, including the fastener holes. Completely rotten frames must be replaced. Completely rotten plywood should be replaced, although smaller areas of deterioration can be repaired using our products.
Evaluation of structural repairs on wooden boats usually requires outside opinions. Get them. We will always be as helpful as we can, especially if pictures are sent as jpeg images. We’ll never tell you to make a repair using our products if we don’t believe that the finished repair will be strong and durable. If new wood is needed, we’ll say so.
Total Hull Renovation:
Glass Over Wood, Sheathing, and Coatings
Using epoxy or polymer products is often contemplated by owners of older wooden boats. In doing so, one must ask oneself exactly why this is being considered. Is it to stop leaking and increase hull durability and finish, or is it to increase the structural characteristics of the hull? The distinction is important.
Using resins and resins/cloth to add structural strength to a hull is not generally a procedure that can be recommended. If the hull needs such treatment, then that means the basic structure of the hull is not sound. The hull should be repaired by traditional means, and in accordance with the original hull specifications. Heavy resin/glass cloth sheathing can and has been used in a few instances, but only by basically building a new hull out of fiberglass and resin over the old wood, and being certain that it has all the proper internal bracing and support. The old wood is considered structurally “irrelevant”. It can be treated with chemistry to stop the deterioration process. It’s a daunting prospect and a complicated process, and not one we would generally recommend.
Coating a hull to stop leaking and for long-term durability is more feasible, but still one that can take a lot of work and preparation, especially of the hull is carvel, double-planked or lapstrake in construction. Plywood and strip-planked hulls are easier because there are no or very few open hull seams.
It is our opinion that epoxy resin alone should never be used on flat, broad surfaces without embedding it in glass cloth. The cloth serves the same purpose as re-bar serves in concrete: It gives structural strength to a compound that is liable to fracture under bending or impact loads. This would be less apt to happen with the General Purpose Epoxy™ Resin, but it is still an issue. It is also our opinion that there should be no permanent coating put on a wooden hull without using S-1™ Clear Penetrating Epoxy Sealer as a prime coating first. This protects the wood and greatly discourages any tendency for the wood to rot should any moisture become trapped between the coating and the wood.
Coating or sheathing a hull should never be done unless the wood is absolutely dry. This means that the boat must be stored under cover for a considerable length of time before the preparation process begins. On a large boat, it may take over a year for the wood to dry to a satisfactory level. Smaller hulls will take less time.
The hull must be bare to original wood, and all repairs made before any coatings are applied. On plywood hulls all seams should be cleaned out and filled with a flexible polyurethane sealant, such as the Dymonic® 100 we sell. The same process would be used on lapstrake hulls and on double-planked hulls. Strip planked hulls can have seams filled with the Sculpwood® Epoxy Paste, since allowances for plank expansion are not a major issue.
Carvel planked hulls present the greatest challenge because the hull is “loosely” constructed and has fairly open seams that are generally caulked with cotton and seam compound. The hulls are designed to move and flex, and to be re-caulked at periodic intervals. This flexing can soon crack or “bubble” a fiberglass sheathing, even if it is embedded in a premium epoxy resin. The preferred method of solving this problem is to “spline” all the seams, which more or less converts the hull into one resembling a strip-planked hull. To do this all seams must be routed out to bare wood, the seams treated with S-1™, spline’s of a soft wood such as cedar or red oak bonded in with an epoxy glue (the G-2™ is an ideal bonding agent here), everything ground smooth and then treated with S-1™. The sheathing or coating process can then begin. Its a detailed and time-consuming process, and must be done under good cover.
There is an option to the resin coatings, based on the fact that resin coatings are rigid and polyurethane coatings are flexible. That option is the Elastuff™ 120 100% Solids Polyurethane Coating and a topcoating. Elastuff™ 120 retains enough flexibility to move with the hull, and yet is tough enough to give the hull a dense, watertight shield. It avoids the whole issue of a fiberglass cloth because none is required. It can be over coated with bottom paint, or with the Elasta-Tuff™ 6000-AL-HS, a polyurethane that is totally UV-resistant and will chemically bond with the Elastuff™ 120. We have been testing polyurethane undercoats and polyurethane top coats together for years and are impressed with their strength and durability. These polyurethanes could be applied over a carvel-planked hull without the splining mentioned above, assuming that the seams were cleaned out totally and caulked with a polyurethane sealant such as the Dymonic® FC or Dymonic® 100 before the first coating of Elastuff™ 120 was applied.
Ask questions. Describe your hull, and we’ll give you all the help that we possibly can. We are available 7 days a week from 6:30 AM to 5:30 PM pacific time Monday–Friday, and 8:30 AM to 5:30 PM PT on weekends and holidays by phone and via email for technical support.