Home > Product Line & Price List > Dymonic® 100

Dymonic® 100
High-Performance, High-Movement Polyurethane Sealant
A bonding sealant for seams, joints and junctions where adhesive strength is of primary importance.
Description
Dymonic 100 is a high-performance, medium-modulus, low-VOC, UV stable, non-sag, caulk-gun applied polyurethane sealant. Formulated with an innovative polymer technology. Dymonic 100 is highly versatile and has a unique capability to adhere to damp or green concrete and does not require a primer on most materials, but it adheres very well to cured epoxy-coated surfaces and fiberglass laminates.
Basic Uses
Dymonic 100 is a durable, flexible, sealant that offers excellent performance in moving joints, is a good all around excellent general purpose sealant that exhibits tenacious adhesion once fully cured. Designed for use on bare wood, epoxy-treated wood, fiberglass laminates, perimeter caulking (windows, doors, panels), concrete and masonry construction joints,aluminum and vinyl siding. Dymonic 100 is designed for interior and exterior use and is suitable for water immersion.
Limitations
Do not apply over damp or contaminated surfaces. Substances that will contaminate a surface include glycols or products suspended in glycol, waxes or products with a wax base, substances that contain or contained silicones. Surfaces should be dry and clean to the base substrate. Penetrating epoxy coatings on the substrate should be fully cured before Dymonic 100 is applied. A full cure of the Dymonic 100 is required for use under a polyurethane deck coating. Use with adequate ventilation.
Packaging
Stocked in 10 oz. (300 ml) gun cartridges.
Stocked Colors
colors are approximate
![]() |
White |
Applicable Standards
Dymoinc 100 meets or exceeds the requirements of the following specifications:
- ASTM C 920 Type S, Grade NS, Class 50, Use NT, T, M, A, O, I
- U.S. Federal Specification TT-S-00230C Class A, Type II
- CAN/CGSB-19, 13-M87
Application Recommendations
May be used in any vertical or horizontal joint, seam or crack. Joint width should be 4 times anticipated movement, but not less than ¼″ (6.4mm). Application tube can be cut to the width of the joint and applied to a depth and width of at least ¼″ by ¼″ (6mm by 6mm). Joints ranging from ½″ to 1″ (13mm to 25mm) wide, the sealant depth should be approximately one-half of the joint width. Closed cell or reticulated polyethylene backer rod or adhesive-backed polyethylene tape can be used to control the depth of the sealant bead on very deep seams.
Surface Preparation
For best adhesion, the joint interface must be sound, clean and dry. The joint surface may require a thorough wire brushing, grinding, sandblasting, or solvent washing. A primer such as S-1™ Clear Penetrating Epoxy Sealer can be used if desired. Primed surfaces should be fully cured before Dymonic 100 is applied.
Application
Dymonic 100 is easy to apply with conventional caulking equipment. Fill joint completely with a proper width-to-depth ratio (see chart below) and tool. Curing happens at the rate of 3/32 inch (2.4 mm) depth per day at 75°F (24°C), 50% R.H., a skin should form within 2 hours and be tack-free in 6–8 hours. The cure rate is lengthened at lower temperatures and less humidity. Dymonic 100 can be painted after it has fully cured.
Tooling & Cleaning
Tooling is recommended immediately after application to insure firm, intimate contact with the joint or seam interface. Dry tooling is preferred, although tooling agents (such as xylene in limited amounts) can be used. Excess sealant and smears adjacent to the joint can be removed with xylene or mineral spirits before sealant cures. After sealant cures excess compound can be cut away with a blade. For a cleaner finish, mask the sides of the joint with a tape prior to filling.
Here is a chart that will help you estimate how many cartridges you will need for any application:
Sealant usage charts in U.S. and Metric measurements.
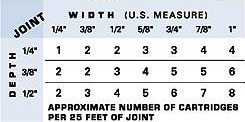
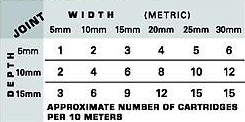
Below is a comparison of the Dymoinc 100 to 3M 5200.
Physical Properties | Dymonic 100 | 3M 5200 |
---|---|---|
Consistency: | Non-Sag, caulkable | Non-Sag, caulkable |
Hardness: (ASTM C 661) | 40 ±5 | 58 |
Tack Free Time: | 6–8 hrs. @ 73°F (23°C), 50% R.H. | 24–48 hrs. @ 70°F (21°C), 50% R.H. |
Service Temperature | -40°F to 180°F (-40°C to 82°C) | -40°F to 190°F (-40°C to 88°C) |
Rate of Cure: | 3/32″ (2.4 mm) per day @ 75°F (24°C), 50% R.H. | ⅛″ (3.2 mm) in 2 days @ 70°F (21°C), 50% R.H. |
Stain & Color Change: | None | - |
Adhesion-in-Peel: | 20–35 pli | - |
Movement Capability: | +100/-50% (ASTM C719) 800 to 900% (ASTM D412) | 800% (ASTM D412) |
Tensile strength: | 350 to 400 psi (ASTM D412) | 700 psi (ASTM D412) |
For additional information, refer to the Dymonic 100 Safety Data Sheet.
PDF Documents
You will need a PDF reader to view these links, you can download Acrobat Reader for free from Adobe’s website.
Safety Data Sheets:
White